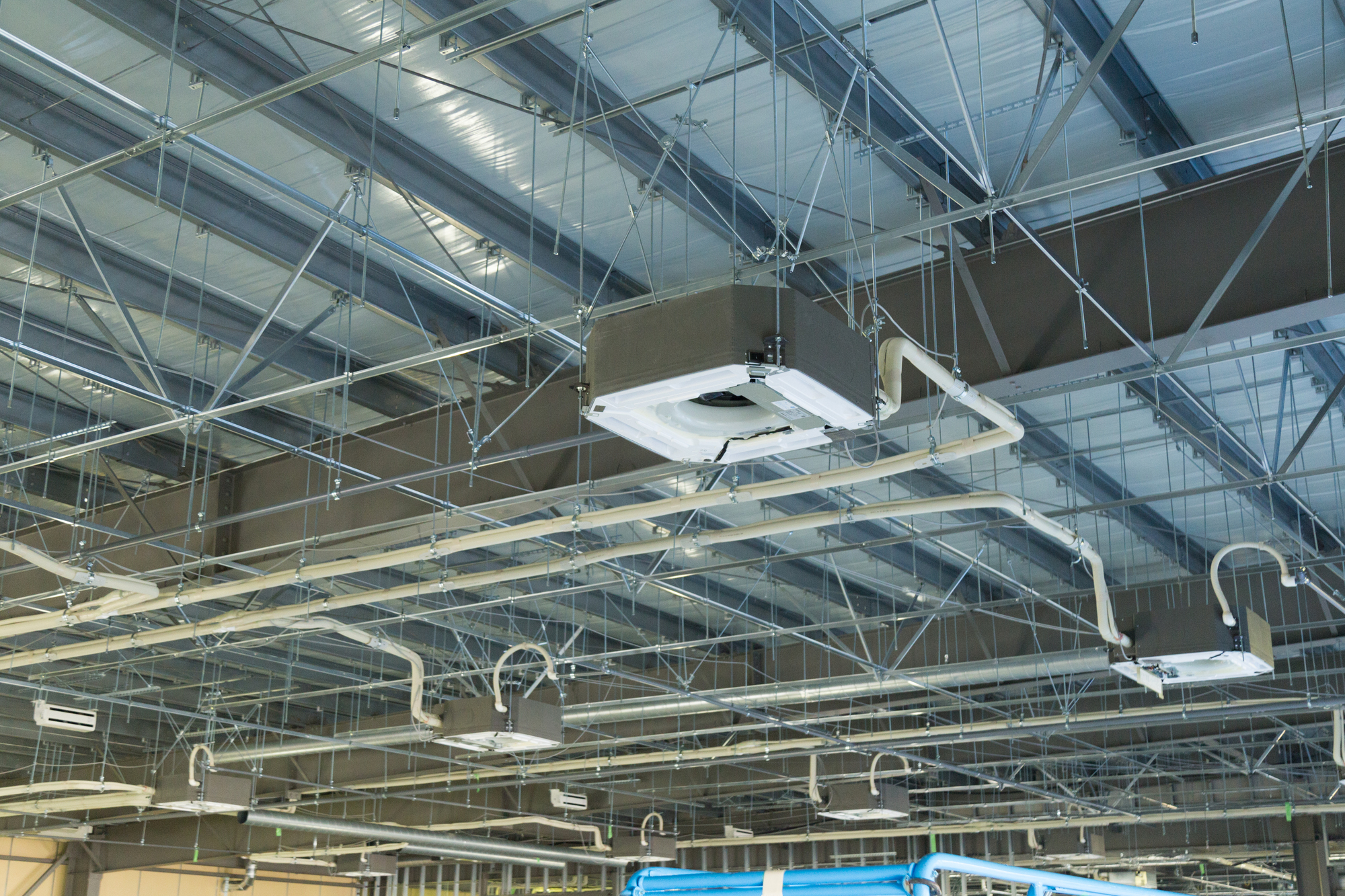
既存工場の不具合部の洗い出し方と注意ポイント
1. 不具合部の洗い出し方
1.現場調査の実施
工場内を細部まで観察し、設備、動線、衛生管理の状況を確認。
写真や動画を活用して記録を残し、改修計画の参考にする。
2.基準との比較分析
HACCPの基準リストを用い、各エリアや設備の適合状況を評価。
不適合項目をチェックリストに基づき抽出。
3.従業員へのヒアリング
現場スタッフから、運用上の問題点や改善希望を聞き取る。
実際に作業を行う従業員の意見を取り入れることで、実用的な改修案を作成。
4.動線・ゾーニングの確認
汚染区域と清潔区域の分離状況や交差汚染防止対策の評価。
実際の物流や人の動線をシミュレーションして問題点を抽出。
5.設備・機器の検査
設備の劣化状況、清掃やメンテナンスのしやすさを検査。
換気や空調、水質管理などのシステムの作動状況もチェック。
2. 注意して確認するポイント
1.ゾーニングと動線管理
清潔区域と汚染区域の物理的分離が徹底されているか。
動線が交差せず、一方向の流れで管理されているか。
2.換気・空調設備
陽圧や陰圧の管理、フィルターの設置状況、定期的な清掃・交換の記録があるか。
温度と湿度の管理が安定しており、微生物の繁殖リスクが抑えられているか。
3.給排水設備
給水のフィルターや殺菌装置が機能しているか。
排水が迅速に処理され、水溜まりや異臭が発生していないか。
4.設備と素材の衛生性
設備や壁、床の素材が清掃しやすく、劣化や破損がないか。
防水、防錆仕様が施されており、食品汚染リスクが最小限に抑えられているか。
5.従業員の衛生管理
手洗い設備や着替えスペースが整備されているか。
衛生教育が行われ、記録が残されているか。
6.記録管理体制
衛生管理記録や点検報告書が適切に保管され、定期的な見直しが行われているか。
まとめ
HACCP基準に基づく改修作業では、不具合の特定と評価項目ごとの徹底した確認が不可欠です。特に、ゾーニングや動線の管理、換気・空調の整備、水質の管理、設備の衛生状態、従業員の教育に重点を置き、現場調査と基準の分析を組み合わせて改修計画を策定することが求められます。
HACCP改修工事の実現方法
HACCP基準に基づく既存工場の改修工事では、初期調査と分析を通じて課題を特定し、それに基づく改善設計を実施します。ゾーニングと動線管理の再配置では、汚染区域と清潔区域の分離を強化し、交差汚染防止策を具体化します。換気・空調システムでは、陽圧・陰圧管理やフィルター強化を施し、温湿度管理を最適化します。
給排水設備では、フィルターや殺菌装置の追加、排水溝の改修を通じて汚染防止策を強化します。さらに、清掃とメンテナンスのしやすい設備と素材を導入し、従業員の衛生管理エリアも充実させます。教育プログラムを整備し、記録管理システムも電子化することで運用を効率化し、継続的な監査体制を構築します。
これらの改修を通じてHACCP基準に適合し、安全で衛生的な製造環境を実現します。